3G 130 Amp. Alternator upgrade for 91 ? 93 5.0 EFI HO MN12s |
 |
 |
Problem: The alternators found on the 5.0 Thunderbirds and Cougars are rated at 70 and some at 90 amperes depending on the vehicle options. At idle, they put out only 15 amps, hardly acceptable for a street car with performance or stereo up grades. So with just minor up grades like inline fuel pump, super-bright headlights, performance ignition system, or your typical stereo amplifiers will put a serious drain on the electrical system. Now add a set of under drive pulleys and watch your voltmeter drop below the NORM at idle in gear.
The fix: Replace that under rated alternator with a 3G 130 amp found on any 94 - 95 5.0 Mustang or 94 - 98 3.8 Mustang with the Mach 460 stereo system. This alt. can be purchased at most automotive parts stores at a fairly reasonable price. If you require an even hotter alternator there are a few manufactures that build even higher rated units using the 3G housing. For instance Best America Ind, http://www.bestamericaind.com can supply an alternator that produces 220 amperes. This is the one I use and I am very satisfied with it.
Not all 3G alternators are 130 amps or have the correct housing. To identify the correct 3G look for the mounting ears spaced 180 degrees apart from each other. The factory or remanufactured units will have an ID tag on the back stating 130 amp or high performance 130 amp. There is no difference between the two so don't let that throw you. They also come with a 60 mm pulley. One of the tricks to get more amps at idle is to install the older Fox body Mustang 70 amp alt. pulley that is 50mm. In order to use this pulley you must place a shim between the pulley and housing or it will bind. This alt. uses the same 3 prong and single prong connectors as used on the MN12s so there is no cutting or splicing necessary. But, there is some machining required.
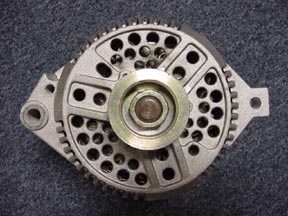 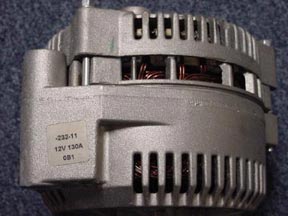
To physically install this alt. you are going to have manufacture a small bracket to allow proper clearance and alignment. I was able to make one out of a piece of 1 x 2 x 6 inch aluminum stock and a piece of 7/8" aluminum round stock. The 3G is physically bigger than the unit on the MN12s besides having it's mounting ears located differently. The bracket makes room for the alt. to fit, keeping it mounted to the same lower location of the original. This allows the use of the same factory length belt and tensioner use.
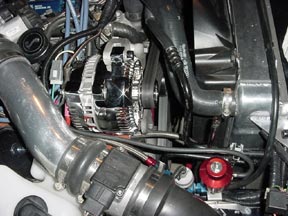 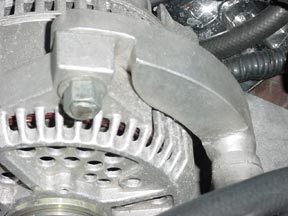
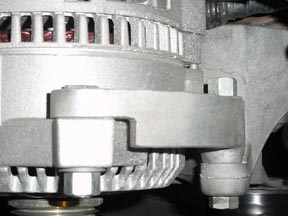
Note: Before starting disconnect your battery. Remove the 3 wires attached to the back of your alternator. Remove the alt. from the engine. By following the simple drawing I have provided you should be able to make your own bracket. The pictures above are of my bracket. I made this in about 30 minutes just eye balling it, no measurements at all. So it looks a little different from the drawing. The following tools, material and equipment are required:
1 piece of 1 x 2 x 6 inch aluminum stock
1 piece of 7/8" aluminum round stock
Two 3/8" bolts, one 1 ?" and one 2 ?", Two 3/8" nuts and 4 washers
Band saw
Drill press or a good half-inch electric drill and vice, Drill bit set
Tig welder
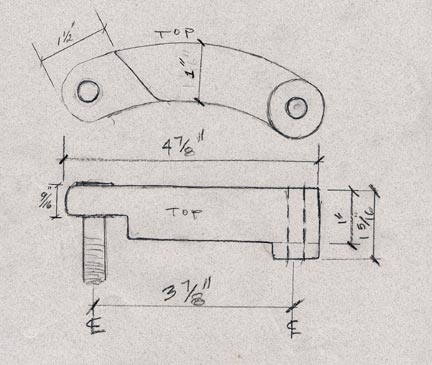
Patent Pending, duplication of this product for profit is prohibited.
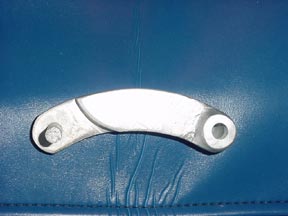 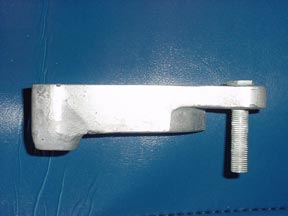
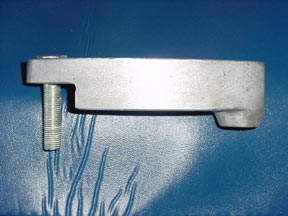 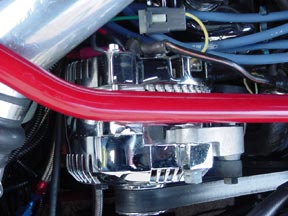
- Draw out the basic shape using the side view on the piece of aluminum.
- Using the band saw cut out the bracket following along the line you just drew.
- Measure 1 ?" from one end of the bracket and mark it.
- Now measure from the same end 2" and mark it.
- Draw a line diagonally across the bracket. This will be the top section of the bracket that attaches to the alt.
- Now looking at the top of the bracket measure 9/16" from the side and mark it.
- If your band saw has a fence set it at 9/16".
- Now cut the insert out from the bracket with two cuts being careful not to cut past your marks.
- Cut the Diagonal line first and then using the fence and the 9/16th line make the final cut.
- Set your fence for 5/16".
- Now take the 7/8" round aluminum stock and measure 5/16" and mark it. This is the spacer needed between the alt. bracket and alt. mount.
- Cut the spacer from the round stock. Ensure it is cut squarely.
- Now place the spacer on the bottom end of the bracket. It should be even centered from the very end of the bracket and the bracket?s top and bottom. The spacer is spaced like this because you?re going to weld it in place. The bead around the circumference of the spacer will make up the small difference between the two pieces.
- Now weld the two together. You only have to weld where the two pieces come together. Don?t bother with trying to build up the spacer to match the bracket.
- Now find the center of the spacer and center punch it. This is easily done by drawing two lines (X) on the spacer.
- First drill a small 1/8" hole all the way through the spacer and bracket, then work your way up to 7/16".
- Test fit the 2 ?" long bolt.
- Install the new alt. at the lower mounting ear to the lower alt. mount on the engine using the long bolt removed from the factory alt. Do not tighten all the way. You want it to move freely for now.
- Now take your new bracket and install it at the top alt. mount on the engine using the 2 ?" long bolt and through the hole you just drilled. Do not tighten; allow the bracket to move freely.
- Now swing the alt. and the bracket together. Find a position between the two that the spacing is uniform. Now mark the bracket where the ear touches. Then take the short bolt and color the very end of it with a crayon and push it through the bolthole up against the bracket. This will leave a location mark on the bracket.
- Remove the bracket and double-check your mark before drilling the hole. Drill the hole the same as the other.
Note: 1. Some of these alt. come with the hole in the upper mounting ear threaded. If you happen to get one of these you can do one of two things. 1. Use a sorter bolt and thread it into the alt. 2. Drill out the hole and follow the described above.
2. I have a Kenny Brown Shock Tower Brace installed. The brace only allowed about 5/16" between it and the alt. bracket. This didn?t allow room for a nut or the head of the bolt. So I drilled the upper hole on the alt bracket just under 3/8", ground the head of the bolt down until there was only 1/16" left. Then applied some Loc Tite in the hole and pressed the bolt into the bracket. This gave me ?" of room between the bolt head and the STB.
- Reinstall the alt. bracket and tighten all the bolts.
- Install the serpentine belt and ensure the pulley is in alignment.
- Now your ready to hook up the alt. electrically
Electrical Properties of Standard Annealed Copper Wire
Bare Wire
Gauge*
AWG |
Diameter
(Nominal)
in |
Area,
Circular Mils |
Ohms/1000
ft |
Ft/ohm |
Amp
Outside
Engine
Space |
Amp
Inside
Engine
Space |
0000 |
0.4600 |
211,600 |
0.04901 |
20,400 |
445 |
378.3 |
000 |
0.4096 |
167,800 |
0.06180 |
16,180 |
385 |
327.3 |
00 |
0.3648 |
133,100 |
0.07793 |
12,830 |
330 |
280.5 |
0 |
0.3249 |
105,500 |
0.09827 |
10,180 |
285 |
242.3 |
2 |
0.2576 |
66,370 |
0.1563 |
6,400 |
210 |
178.5 |
4 |
0.2043 |
41,740 |
0.2485 |
4,025 |
160 |
136 |
6 |
0.1620 |
26,250 |
0.3951 |
2,531 |
120 |
102 |
8 |
0.1285 |
16,510 |
0.6282 |
1,592 |
80 |
68 |
10 |
0.1019 |
10,380 |
0.9989 |
1,001 |
60 |
51 |
12 |
0.08081 |
6,530 |
1.588 |
630 |
45 |
38.3 |
14 |
0.06408 |
4,107 |
2.525 |
396 |
35 |
29.8 |
16 |
0.05082 |
2,583 |
4.016 |
249 |
25 |
21.3 |
18 |
0.04030 |
1,624 |
6.385 |
157 |
20 |
17 |
20 |
0.03196 |
1,022 |
10.15 |
98.5 |
- |
- |
22 |
0.02535 |
642.4 |
16.14 |
61.95 |
- |
- |
Electrical installation: But for you get started there?s a few things you need to know and I recommend you install. The alternator output wire (black/orange) is only 6 gage and then runs to a fusible link that is only 12 gage. From this link the wire becomes 8 gage as illustrated in the above Ford drawing. Now I don?t know where Ford came up with their wire size rating. But, when I looked at the wires on my car they measured out 8 gage from the alt. the fusible link was correct and from the link to the solenoid was 10 gage. Using the chart I provided for wire amperage rating by gage you can see that these wires capable of handling the potential current that could be supplied from the 3G 130 amp alt. They aren?t even large enough to handle the output of the stock alt.
To correct this I installed a 4 gage wire from the alt. output terminal to the positive side of the battery. I also left the stock black/orange wire connected. I purchased the wire from PA Performance www.pa-performance.com it came with all the ends made up and an inline 200 amp fuse. See pictures below. Or you can make your own wire lead. I think the 200 amp fuse is a little over kill and recommend replacing it with a 125 amp. These fuses will not blow at the rating indicated. Fuses do not blow at their rated value. With a 125 amp fuse, the time it takes it to blow is depends on the current flow as a percentage of the fuse's rating. At 140% (175amps) of this fuse's rating, it will take it 200 seconds to blow. At 180% (225amps), it will take 6 seconds; at 280% (350amps), it takes 1 second.
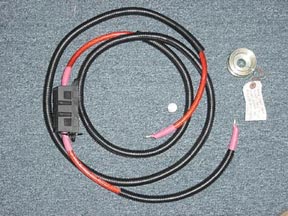 216>
- Insert the large black plug and the small gray plug into their corresponding jacks at the back of the alt.
- Place the 4 gage lug over the alt. output terminal, then the factory black/orange wire on top of that. Install the nut and tighten, being careful not to over tighten and breaking the terminal loose.
- Run the 4 gage wire along the passenger?s side forward to under the radiator support.
- Remove the radiator mounting bolts and swing the radiator rearward just enough to allow access to the wire way behind it.
- Run the 4 gage wire along the wire way and secure it with plastic tie wraps.
- Reinstall the radiator and bolts.
- Depending on the type of battery you have install the other end of the 4 gage wire that has the fuse attached, to the battery positive (+) post.
- Finish connecting the battery leads.
- Check over your work, making sure all connections are good, bolts and belt are tight. And all your tools are out of the way.
- Start the engine, check your voltage output, it should be 14.5 ? 13 VDC.
Lonnie Doll
Sponsor Links |
 |
 |
|
|
|
|

|